The construction industry is continually evolving, and one of the most exciting developments in recent years is the rise of prefabrication and modular construction. These approaches are revolutionizing how buildings are designed, constructed, and delivered, and at the heart of this transformation is Building Information Modeling (BIM). In this blog, we will explore how BIM is enhancing the prefabrication and modular construction processes, improving efficiency, reducing costs, and enabling faster project delivery.
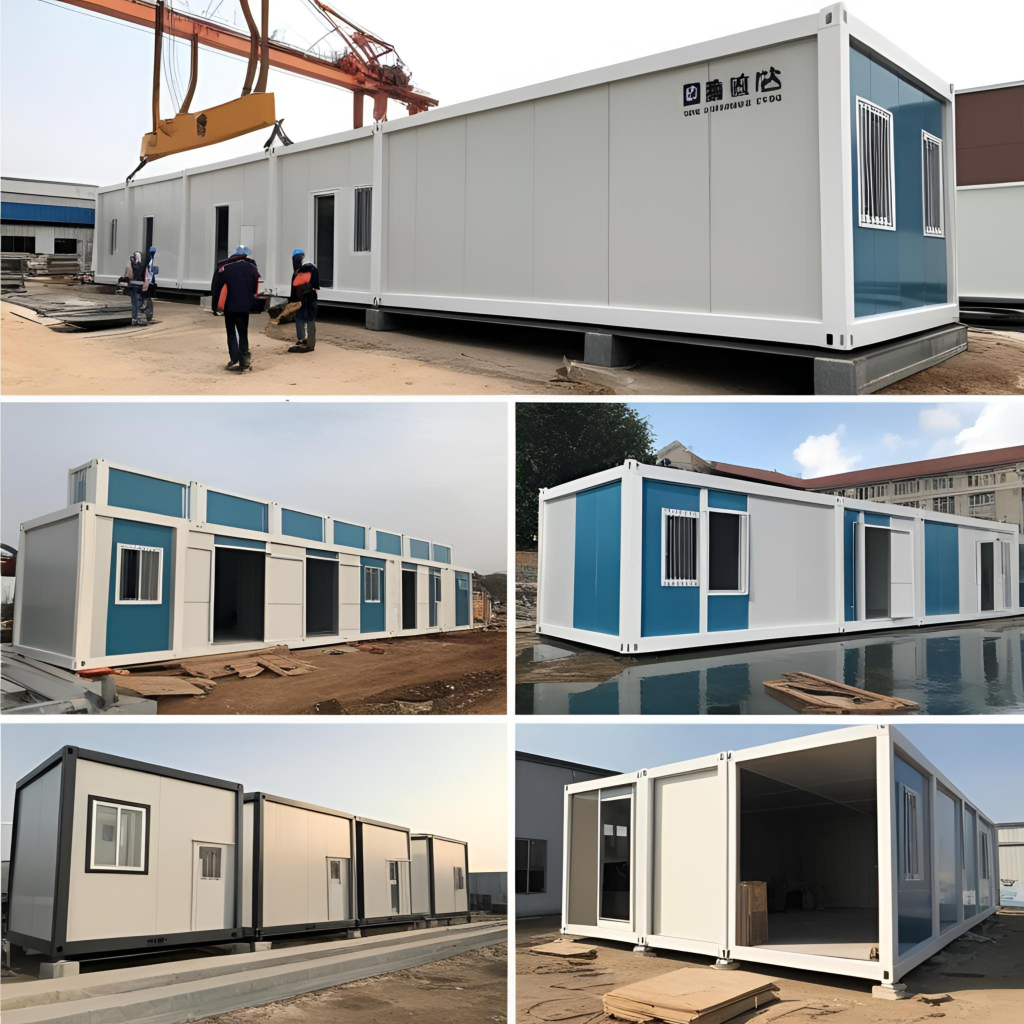
What is Prefabrication and Modular Construction?
Prefabrication and modular construction are innovative building methods that involve assembling building components off-site in a controlled factory environment, which are then transported and assembled on-site. These methods offer several advantages, such as:
- Faster construction times due to parallel work processes.
- Higher quality control due to a controlled, indoor manufacturing environment.
- Reduced labor costs with factory-based assembly.
- Less waste from more precise construction processes.
In modular construction, entire sections or modules of a building are pre-constructed and then assembled on-site. In prefabrication, individual components (like walls, floors, or roofs) are manufactured off-site and assembled on-site, but these components are often smaller and may require more on-site construction for assembly. While these methods were once considered niche, their popularity is growing rapidly, driven by their ability to streamline construction and offer more sustainable, cost-effective solutions. This is where BIM comes in.
How BIM Transforms Prefabrication and Modular Construction
1. Improved Design Coordination – One of the primary benefits of BIM in modular and prefabricated construction is its ability to enhance design coordination. In traditional construction, communication between architects, engineers, contractors, and suppliers can be fragmented, leading to errors and delays. BIM, however, provides a shared digital platform where all stakeholders can collaborate in real time. For prefabrication and modular construction, this means that every component—whether it’s a wall panel, structural beam, or electrical system—can be accurately modeled and coordinated before fabrication begins. BIM allows designers and engineers to detect potential issues early, such as misalignments, clashes, or errors in the design, reducing the need for costly and time-consuming corrections during construction.
Example: A BIM model allows architects and contractors to visualize the complete layout of prefabricated modules, ensuring that everything fits together before it’s manufactured. This minimizes on-site adjustments and accelerates construction.
2. Enhanced Prefabrication and Manufacturing – BIM significantly improves the manufacturing process of prefabricated components. By providing a detailed, accurate 3D model of each part, BIM ensures that the components are manufactured with precision. This reduces the likelihood of errors during the prefabrication process and leads to higher-quality components. Manufacturers can use BIM to generate detailed shop drawings, which guide the production of prefabricated elements. These drawings provide all the necessary measurements, materials, and assembly instructions, ensuring that each piece is produced to the correct specifications.
Example: For a modular construction project, BIM data can be used to produce precise cutting lists for steel or timber components, reducing material waste and ensuring that each part is ready for assembly as soon as it arrives on-site.
3. Streamlined Logistics and Delivery – In modular and prefabricated construction, managing the logistics of delivering the right materials and components to the right place at the right time is crucial. BIM plays an essential role in optimizing this process by tracking and scheduling the delivery of each prefabricated element. BIM’s ability to provide real-time data on production schedules, transportation, and on-site needs means that components can be delivered in a timely manner, reducing delays caused by waiting for materials to arrive. Furthermore, BIM enables better planning of on-site assembly, ensuring that the modules and components are delivered in the correct sequence for efficient construction.
Example: A project manager can use BIM to track the delivery of prefabricated modules, ensuring that they arrive at the construction site in the correct order and at the right time, minimizing delays and the need for on-site storage.
4. Accurate Scheduling and Project Planning – With BIM, project teams can integrate 3D modeling with scheduling software (such as 4D BIM) to visualize how a project will progress over time. For modular and prefabricated construction, this means that project managers can simulate the entire construction process, from the fabrication of components to on-site assembly. Using BIM for scheduling allows teams to create realistic timelines that factor in off-site construction, shipping, and on-site assembly. This ensures that the project stays on track and is delivered on time, with fewer delays or setbacks.
Example: Using 4D BIM, a project manager can visualize the entire process, from prefabrication to assembly, helping identify potential scheduling conflicts and resolve them before construction begins.
5. Better Cost Control and Waste Reduction – One of the most significant benefits of BIM in modular and prefabricated construction is cost control. By using BIM for detailed design, quantity takeoffs, and material management, contractors can more accurately estimate costs and track expenses throughout the project lifecycle. Moreover, because prefabrication and modular construction involve manufacturing components off-site in a controlled environment, waste is reduced. BIM helps ensure that materials are used efficiently, minimizing over-ordering and excess waste. It also enables accurate tracking of material deliveries, further reducing the chances of over-purchasing.
Example: With BIM, contractors can perform precise quantity takeoffs that account for every material needed in the modular components. This leads to more accurate procurement, reducing the chances of unnecessary materials being purchased or left unused.
6. Improved Collaboration and Communication – One of the standout features of BIM is its ability to improve collaboration between all stakeholders involved in a project. In modular and prefabricated construction, multiple teams—designers, manufacturers, contractors, and suppliers—must work together seamlessly to ensure the project progresses smoothly. BIM serves as a single source of truth for all parties involved, allowing them to view, share, and update the project model in real time. This enhances communication, ensures that everyone is working from the same data, and reduces the risk of misunderstandings or errors.
Example: If a design change is made to a prefabricated module, the updated model is instantly available to all relevant stakeholders, from manufacturers to construction teams, ensuring that the change is implemented correctly across all stages.
Benefits of BIM in Prefabrication and Modular Construction
1. Faster Project Delivery – By streamlining design, manufacturing, logistics, and scheduling, BIM accelerates the overall construction timeline. With prefabrication and modular construction methods, much of the work is done off-site, allowing for simultaneous activities, such as foundation work and module fabrication. This parallel processing significantly shortens project delivery times.
2. Enhanced Quality Control – BIM ensures that every part of the prefabrication and modular construction process is well-coordinated and accurately manufactured. This results in higher-quality components, fewer errors on-site, and better overall building performance.
3. Cost Savings – By improving planning, reducing material waste, and optimizing schedules, BIM can lead to significant cost savings in modular and prefabricated projects. Accurate budgeting and forecasting also help avoid financial overruns.
4. Improved Sustainability – BIM helps reduce construction waste by enabling more accurate material usage and optimizing the fabrication process. Additionally, modular buildings are often more energy-efficient due to the precision with which components are constructed.
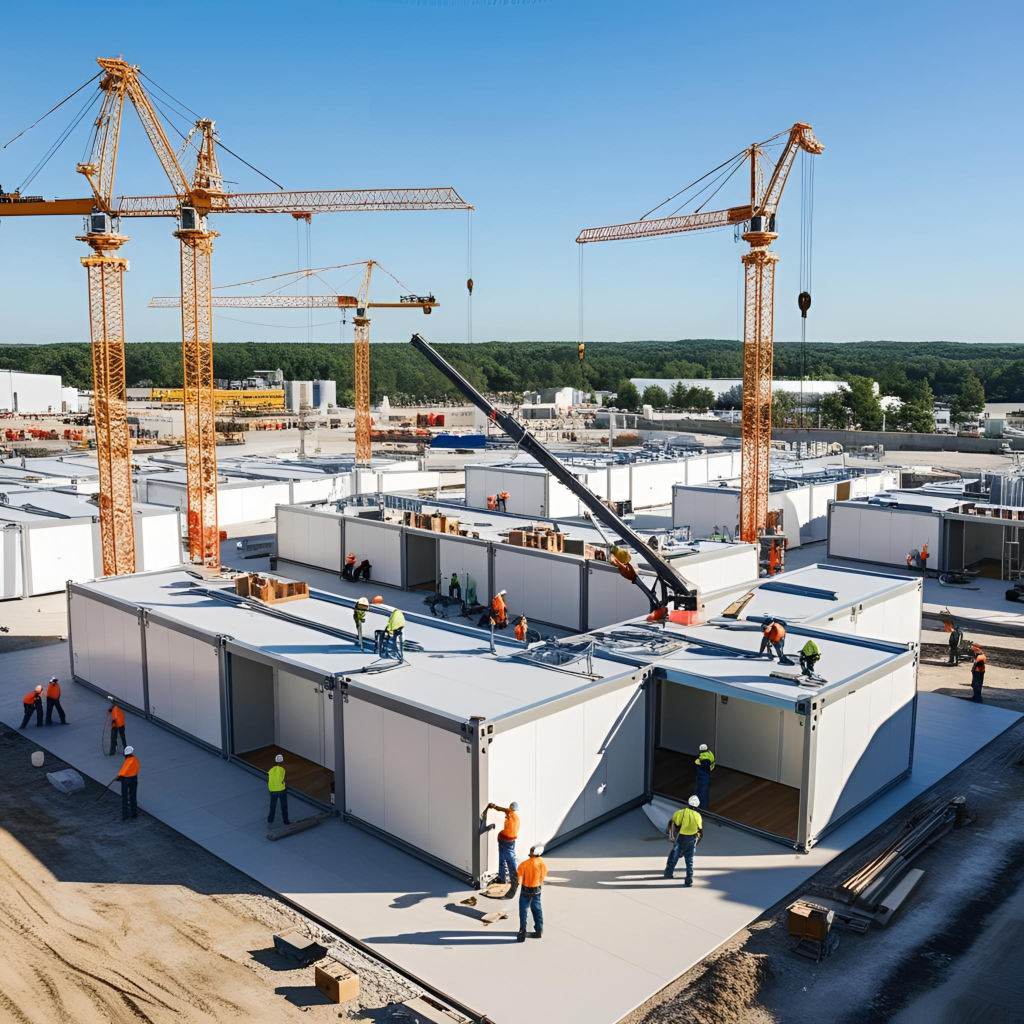
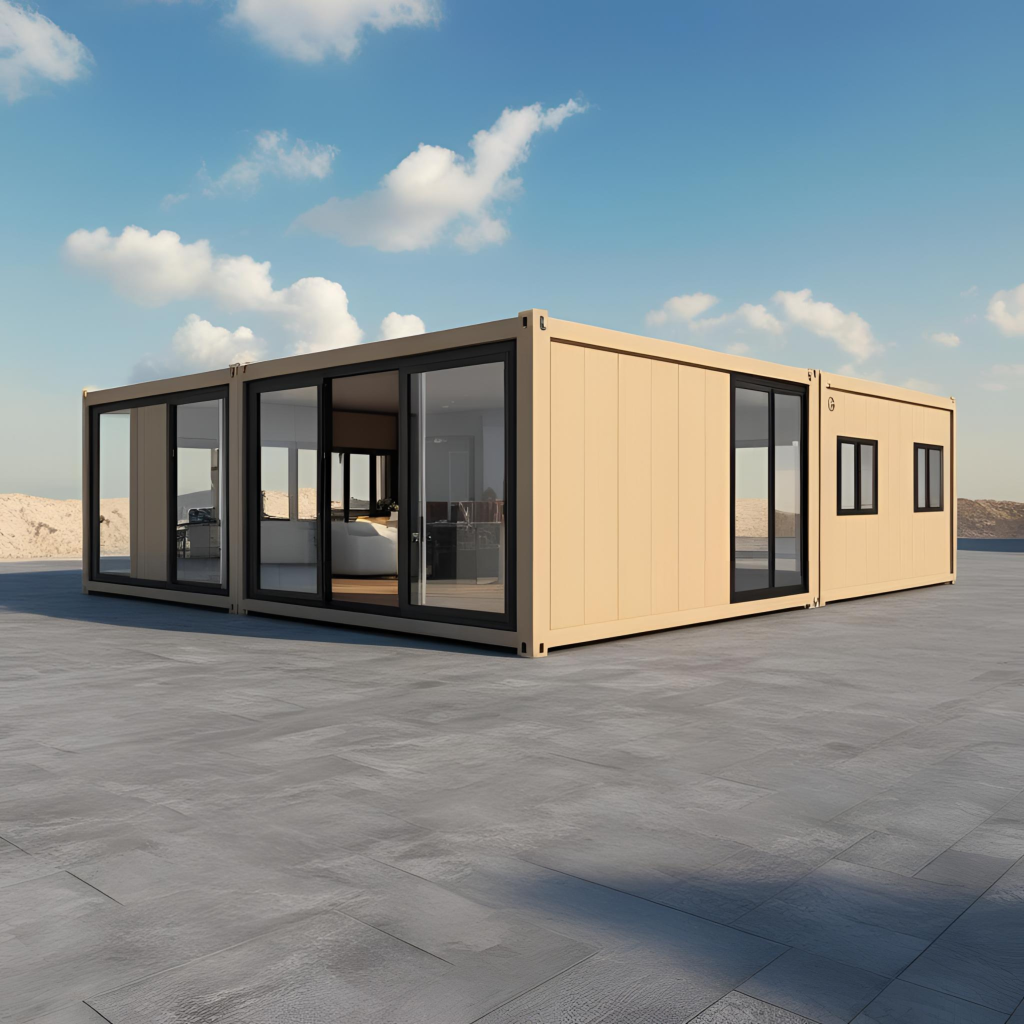
Challenges of Implementing BIM in Modular and Prefabricated Construction
1. Initial Investment – The upfront costs of implementing BIM technology can be high, particularly for smaller construction firms. However, these costs are usually offset by the long-term savings in efficiency, quality, and reduced rework.
2. Technology Integration – Integrating BIM with existing manufacturing processes can be challenging. Some construction firms and manufacturers may need to invest in new software, hardware, or training to fully realize the benefits of BIM in modular and prefabricated construction.
3. Skill Gaps – To fully utilize BIM in modular construction, a skilled workforce is necessary. Teams need to be trained in both BIM technology and the specifics of prefabrication and modular construction to ensure the process runs smoothly.
Conclusion
BIM is playing a pivotal role in transforming prefabrication and modular construction. By improving design coordination, optimizing manufacturing processes, enhancing logistics, and enabling real-time collaboration, BIM helps reduce costs, improve quality, and speed up the construction process. As the construction industry continues to evolve, BIM will remain at the forefront, driving innovation and efficiency in the prefabricated and modular construction sectors.